Überblick über die additive Fertigung mit EBM
Beim Elektronenstrahlschmelzen (EBM) handelt es sich um eine Art der additiven Pulverbettschmelzfertigung, bei der mithilfe eines Elektronenstrahls metallische Pulverpartikel Schicht für Schicht selektiv geschmolzen und verschmolzen werden, um komplexe 3D-Teile aufzubauen.
Zu den Hauptmerkmalen des EBM-Prozesses gehören:
- Erstellt vollständig dichte Teile aus Metallpulver-Ausgangsmaterial
- Verwendet einen Elektronenstrahl als Energiequelle
- Funktioniert unter Vakuum und hoher Temperatur
- Erzielt hervorragende mechanische Eigenschaften
- Ideal für reaktive Metalle wie Titan und Tantal
- Ermöglicht komplexe Geometrien, die mit maschineller Bearbeitung nicht möglich sind
- Um das endgültige Finish des Teils zu erreichen, kann eine Nachbearbeitung erforderlich sein
EBM bietet die Vorteile von Designfreiheit, Teilekonsolidierung, reduziertem Gewicht und Leistungsverbesserungen in den Bereichen Luft- und Raumfahrt, Medizin, Zahnmedizin, Automobil und Industrie.
Wie EBM Additive Fertigung Funktioniert
Der additive Fertigungsprozess EBM funktioniert wie folgt:
- Ein 3D-CAD-Modell wird in dünne Querschnittsschichten geschnitten.
- Metallpulver wird gleichmäßig über eine Bauplatte in der Vakuumkammer verteilt.
- Ein Elektronenstrahl scannt das Pulver selektiv und schmilzt es basierend auf den Schnittdaten.
- Die Bauplatte fällt herunter und eine weitere Schicht Pulver wird darüber verteilt.
- Wiederholen Sie die Schritte 3-4, bis das Teil fertig ist.
- Überschüssiges Pulver wird entfernt und das Teil wird wärmebehandelt.
- Bei Bedarf können Nachbearbeitungen wie spanende Bearbeitung oder Bohren durchgeführt werden.
Die EBM-Maschine steuert den Elektronenstrahl mithilfe elektromagnetischer Linsen und Ablenkspulen präzise. Der Prozess findet unter Hochvakuum statt, was sehr hohe Schmelztemperaturen ermöglicht.
Arten von EBM-Systemen für die additive Fertigung
Es gibt zwei Haupttypen von EBM-Maschinen:
Maschinentyp | Beschreibung | Größe bauen | Materialien | Anwendungen |
---|---|---|---|---|
Kleine Systeme | Geringere Kosten, geeignet für Kleinteile | 150 x 150 x 150 mm | Titan, Kobalt-Chrom, Edelstahl, Werkzeugstahl | Zahnmedizin, Medizin, Forschung |
Große Systeme | Für Anwendungen in der Großserienproduktion | 500 x 400 x 400 mm | Titan, Inconel, Tantal | Luft- und Raumfahrt, Automobil, Industrie |
Arcam EBM und GE Additive sind die größten Hersteller von EBM-Systemen, die sowohl kleine als auch große Maschinen anbieten.
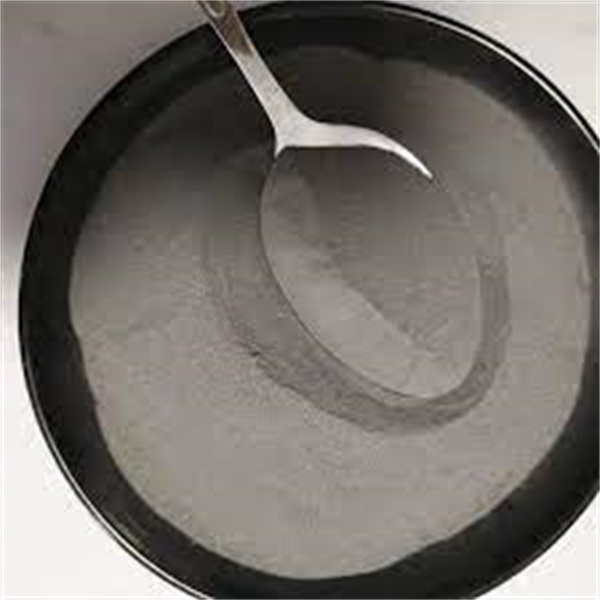
Materialien für die additive EBM-Fertigung
Mit der EBM-Technologie können eine Reihe von Metallen bearbeitet werden:
- Titan-Legierungen: Ti6Al4V, Ti6Al4V ELI, TiAl
- Nickel-Legierungen: Inconel 718, Inconel 625
- Kobalt-Chrom-Legierungen: CoCrMo
- Stähle: Edelstähle, Werkzeugstähle, Maraging-Stähle
- Hochschmelzende Metalle: Tantal, Wolfram
- Edelmetalle: Silber, Gold, Platin
- Aluminium-Legierungen: AlSi10Mg
Titan ist aufgrund seiner Reaktivität besonders für EBM geeignet. Aber auch aus anderen fortschrittlichen Legierungen können mit dem Verfahren hochfeste und korrosionsbeständige Teile hergestellt werden.
Anwendungen der additiven EBM-Fertigung
Zu den wichtigsten Anwendungen gehören:
Luft- und Raumfahrt: Turbinenschaufeln, Triebwerkskomponenten, Flugzeugzelle und Strukturteile
Medizinische Implantate: Orthopädische Implantate, Fixierungsgeräte, chirurgische Instrumente
Automobilindustrie: Turboladerräder, Ventilkörper, Teile des Kraftstoffsystems
Industriell: Wärmetauscher, Druckbehälter, Pumpengehäuse, Vorrichtungen und Vorrichtungen
Öl und Gas: Bohrlochwerkzeuge, Ventilkörper, Verteiler
Verteidigung: Satelliten- und UAV-Komponenten, Panzerung
EBM ermöglicht in diesen Branchen leichtere, stärkere und leistungsfähigere Komponenten mit optimierten Designs.
Vorteile von EBM Additive Fertigung
Zu den Vorteilen der EBM-Technologie gehören:
- Geringe Porosität – Die Annäherung an die Dichte 100% führt zu hervorragenden mechanischen Eigenschaften
- Hohe Festigkeit – Titanlegierungen erreichen die Eigenschaften von Knetwerkstoffen und übertreffen diese sogar
- Gestaltungsfreiheit – Komplexe Geometrien können hergestellt werden
- Schnelles Prototyping – Beschleunigt Produktentwicklungszyklen
- Teilweise Konsolidierung – Reduziert Baugruppen durch die Integration mehrerer Komponenten
- Gewichtsreduzierung – Leichtere Komponenten ermöglichen Kraftstoffeinsparungen in der Automobil- und Luftfahrtindustrie
- Just-in-time-Produktion – Reduziert lange Lieferzeiten für Guss- und Schmiedeteile
- Sonderanfertigungen – Patientenspezifische Medizinprodukte und personalisierte Konsumgüter
- Nachhaltige Produktion – Reduziert den Abfall im Vergleich zu subtraktiven Methoden
Diese Vorteile fördern die branchenübergreifende Einführung von EBM, um die Leistung zu verbessern, Kosten zu senken und neue Produktinnovationen zu ermöglichen.
Einschränkungen der additiven EBM-Fertigung
EBM hat einige Einschränkungen:
- Hoher Ausrüstungsaufwand – EBM-Maschinen haben hohe Vorabinvestitionskosten im Bereich von $500.000 bis $1,5 Millionen
- Einschränkungen hinsichtlich der Teilegröße – Bauhüllen schränken die maximalen Teileabmessungen ein
- Dimensionale Genauigkeit – Oft ist eine Nachbearbeitung erforderlich, um enge Toleranzen zu erreichen
- Oberflächengüte – Der Treppenstufeneffekt führt zu rauen Oberflächen, die einer Nachbearbeitung bedürfen
- Baurate – Langsamer als Pulverbettschmelzverfahren mit Laser- oder Elektronenstrahlen
- Reaktive Metalle – Beschränkt auf inerte Metalle oder Metalle wie Titan und Tantal
- Pulverentfernung – Nicht verwendetes Metallpulver muss entfernt und recycelt werden
- Thermische Spannungen – Kann zu Verformungen und Rissen an Teilen führen
Kontinuierliche Entwicklungen in der EBM-Technologie zielen darauf ab, Geschwindigkeit, Qualität, Materialflexibilität und Kosteneffizienz zu verbessern.
Designprinzipien für die additive Fertigung mit EBM
Die Einhaltung von Designrichtlinien ist für den erfolgreichen Einsatz der EBM-Technologie von entscheidender Bedeutung:
- Minimieren Sie Überhänge und nicht unterstützte Geometrien
- Fügen Sie kleine Löcher (1–2 mm) ein, um überschüssiges Pulver zu entfernen
- Nutzen Sie Gitterstrukturen, um das Gewicht zu reduzieren
- Wandstärken über 1 mm beibehalten
- Berücksichtigen Sie Winkel ≥ 30°, um Spannungskonzentrationen zu vermeiden
- Berücksichtigen Sie den linearen Skalierungsfaktor 0,2%
- Lassen Sie bei feinen Details eine Toleranz von 0,2 mm zu
- Entwerfen Sie interne Kanäle ≥ 2 mm für Pulverfreiheit
- Minimieren Sie Bereiche, in denen sich Pulver ansammelt
- Positionieren Sie das Teil auf der Platte, um die Querschnittsfläche zu minimieren
Mithilfe von Simulationstools können Sie die Designleistung schon früh im Designprozess beurteilen. Designs können speziell für AM-Funktionen optimiert werden.
Prozessparameter für EBM
Zu den kritischen EBM-Prozessparametern gehören:
- Strahlleistung – Beeinflusst die Aufbaugeschwindigkeit, Porosität und Mikrostruktur
- Strahlgeschwindigkeit – Höhere Geschwindigkeiten erhöhen die Baugeschwindigkeit, können jedoch die Dichte beeinträchtigen
- Strahlfokus – Fokussierung und Ablenkungskontrollfusion
- Scan-Strategie – Durch die abwechselnde Rasterrichtung zwischen den Schichten werden Eigenspannungen reduziert
- Schichtdicke – Feinere Schichten verbessern die Auflösung, verringern jedoch die Aufbaugeschwindigkeit
- Temperatur aufbauen – Höhere Temperaturen verringern die Eigenspannungen, beeinträchtigen jedoch die Präzision
- Größe des Schmelzbades – Beeinflusst die lokale Mikrostruktur und Eigenschaften
- Rohstoff – Die Größenverteilung und Morphologie des Pulvers beeinflusst Dichte und Oberflächenbeschaffenheit
Durch die Steuerung dieser Parameter können Eigenschaften und Qualität für bestimmte Anwendungen eingestellt werden.
Nachbearbeitung für EBM-Teile
Zu den üblichen Nachbearbeitungsschritten für EBM-Teile gehören:
- Pulverentfernung – Perlstrahlen, um überschüssiges Pulver aus inneren Hohlräumen zu entfernen
- Stressabbau – Heißisostatisches Pressen kann helfen, Eigenspannungen zu reduzieren
- Abgeschnitten – Drahterodiermaschine zum Entfernen von Teilen von der Bauplatte
- Bearbeitung – CNC-Fräsen, Drehen, Bohren zur Erzielung von Maßgenauigkeit und Oberflächengüte
- Polieren – Für glänzende Oberflächen auf optischen Teilen wie Schmuck und medizinischen Implantaten
- Beschichtungen – Aufbringen verschleißfester, reibungsarmer oder ästhetischer Beschichtungen
- Qualitätsprüfung – Messen Sie mechanische Eigenschaften, interne Defekte und Mikrostruktur
Durch die Minimierung der Nachbearbeitung werden die Gesamtkosten der Teile gesenkt. Bei kritischen Anwendungen kann jedoch eine umfangreiche Nachbearbeitung erforderlich sein, um die Spezifikationen zu erfüllen.
Qualitätskontrolle für EBM
Strenge Qualitätskontrollverfahren für die EBM-Produktion umfassen:
- Rohmaterialinspektion – Siebanalyse, Durchflussprüfung und Mikroskopie von Rohmaterialpulver
- In-Prozess-Überwachung – Schmelzbadgröße, Pulverbetttemperatur, Vakuumniveau
- Maßprüfungen – KMG und andere messtechnische Prüfungen kritischer Maße
- Mechanische Prüfung – Zug, Druck, Mikrohärte, Bruchzähigkeit, Ermüdung
- Zerstörungsfreie Bewertung – Röntgen-Computertomographie zur Prüfung auf interne Defekte
- Metallographie – Mikrostrukturelle Charakterisierung mittels optischer und Elektronenmikroskopie
- Dichteanalyse – Archimedes-Methode oder Heliumpyknometrie zur Überprüfung einer Dichte von ≥ 99,5%
- Messung der Oberflächenrauheit – Optische Profilometrie zur Quantifizierung der Oberflächentextur
- Chemische Analyse – ICP und Massenspektroskopie zur Überprüfung der Zusammensetzung
- Validierungs-Builds – Test-Builds zur Überprüfung der Prozessparameter für neue Teile
Diese umfassenden Tests verifizieren die Produktqualität von EBM für anspruchsvolle industrielle Anwendungen.
Kostenmodellierung für EBM Additive Fertigung
Die Gesamtkosten hängen ab von:
- Maschinenkosten – Hohe Investitionen in die Ausrüstung
- Materialkosten – Pulverrohstoffkosten/kg
- Betriebskosten – Arbeit, Energie, Wartung, Inertgas
- Nachbearbeitung – Zusätzliche Bearbeitung und Endbearbeitung
- Bauen Sie Geschwindigkeit auf – Schnellere Builds senken die Kosten
- Nutzungsrate – Eine höhere Maschinennutzung verteilt die Kosten auf mehr Teile
- Buy-to-fly-Verhältnis – Nicht verwendetes Pulver muss recycelt werden, was zusätzliche Kosten verursacht
- Teilegeometrie – Kompakte Teile maximieren die Nutzung des Bauvolumens
- Volumen aufbauen – Größere Maschinen ermöglichen einen höheren Durchsatz
- Größenvorteile – Die Produktion hoher Stückzahlen reduziert die Kosten pro Teil
Mit steigenden Produktionsmengen sinken die Kosten erheblich und überschüssiges Pulver kann wiederverwendet werden.
Auswahl eines EBM-Anbieters für additive Fertigung
Kriterien zur Auswahl eines EBM-Dienstleisters:
- Bewährte Systeminstallationen und Kundenreferenzen
- Vielfältige zertifizierte Erfahrung in den Bereichen Luft- und Raumfahrt, Medizin und Industrieanwendungen
- Auswahl an qualifizierten Materialien wie Titan, Inconel, Kobalt-Chrom
- Zertifizierung des Qualitätsmanagementsystems – ISO 9001, AS9100
- Strenge Prüfverfahren zur Qualitätskontrolle
- Bestand an Standard- und Spezialpulvern
- Sekundäre interne Bearbeitungs- und Endbearbeitungsmöglichkeiten
- Designunterstützung und Build-Simulationsdienste
- Professionelle Ingenieure mit Fachkenntnissen in der Metallurgie
- Große Bauräume für hohen Durchsatz
- Wettbewerbsfähige Preisstruktur transparent kommuniziert
- Kann ITAR und andere regulierte Projekte verwalten
- In der Nähe gelegen, sodass persönliche Treffen und Zusammenarbeit möglich sind
Etablierte Dienstleister mit einer Erfolgsbilanz in regulierten Branchen erfüllen in der Regel die strengen Qualitätsanforderungen am besten.
Vor- und Nachteile von EBM im Vergleich zu anderen AM-Methoden
Vorteile von EBM:
- Völlig dichte Metallteile, die mit Schmiedeeigenschaften mithalten können
- Gute Oberflächengüte auf nach oben gerichteten Flächen
- Hohe Aufbaurate im Vergleich zu Laserverfahren
- Geringe Eigenspannungen im Vergleich zum Laser-Pulverbettschmelzen
- Hervorragende mechanische Eigenschaften der fertigen Bauteile
- Die Kontrolle des Schmelzbades ermöglicht eine Verfeinerung der Mikrostruktur
- Inerte Baubedingungen, ideal für reaktive Metalle wie Titan
- Kostengünstig für mittlere bis hohe Produktionsmengen
Nachteile von EBM:
- Höhere Ausrüstungskosten als Polymersysteme
- Begrenzte Materialoptionen im Vergleich zu Laser-PBF
- Kontrollierter Prozess, der geschulte Bediener erfordert
- Erhebliche Nachbearbeitung oft erforderlich
- Verbraucht große Mengen an elektrischer Energie
- Maximale Teilegröße durch Bauraum begrenzt
- Handhabung und Recycling reaktiver Metallpulver
- Geringere Profilgenauigkeit als bearbeitete oder geschmiedete Teile
Bei der Produktion von Metallkomponenten mit mittlerem bis hohem Volumen zeichnet sich EBM dadurch aus, dass es hohe Festigkeit und Qualität zu angemessenen Kosten liefert. Es erfordert jedoch Erfahrung, den Prozess zu beherrschen.
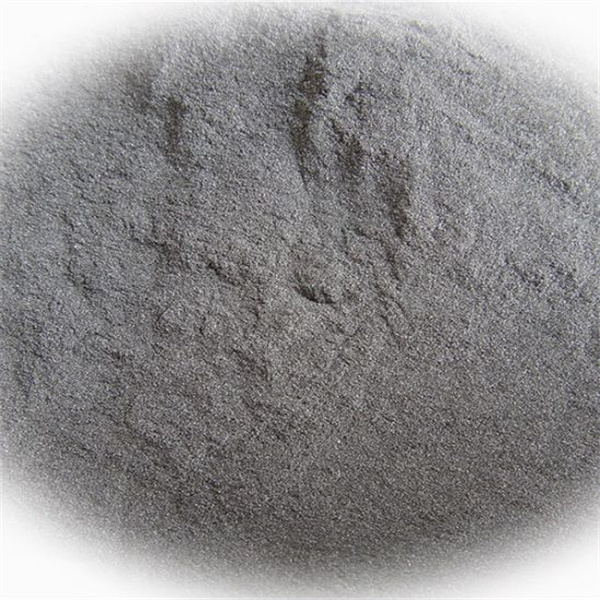
Vergleich von EBM vs. DMLS und SLM
EBM vs. DMLS:
Parameter | EBM | DMLS |
---|---|---|
Strahlquelle | Elektronenstrahl | Faserlaser |
Atomsphäre | Vakuum | Inertes Gas |
Typische Materialien | Titanlegierungen, Tantal, Inconel | Edelstahl, Kobaltchrom, Aluminium |
Baurate | Hoch | Mittel |
Oberflächengüte | Mäßig | Sehr hoch |
Kosten pro Teil | Mäßig | Hoch |
Maximale Teilegröße | Groß | Mittel |
EBM vs. SLM:
Parameter | EBM | SLM |
---|---|---|
Strahlquelle | Elektronenstrahl | Faserlaser |
Atmosphäre | Vakuum | Inertes Gas |
Typische Materialien | Titan, Tantal, Inconel | Aluminiumlegierungen, Stähle, Nickellegierungen |
Verbleibender Stress | Niedrig | Hoch |
Mechanische Eigenschaften | Ausgezeichnet | Sehr gut |
Kosten pro Teil | Mäßig | Niedrig |
Genauigkeit | Mäßig | Hoch |
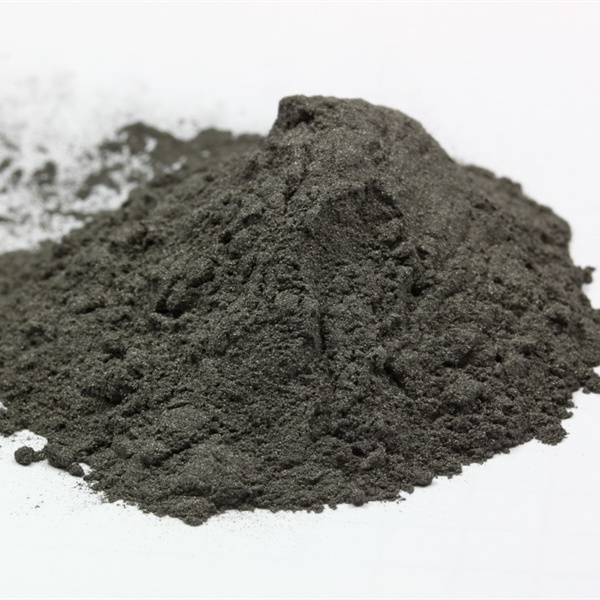
FAQ
Welche Materialien können mit der EBM-Technologie bearbeitet werden?
Die gebräuchlichsten EBM-Materialien sind Titanlegierungen, Nickellegierungen wie Inconel, Kobalt-Chrom und einige Werkzeugstähle. In jüngerer Zeit werden auch hochschmelzende Metalle und Aluminiumlegierungen eingesetzt.
Welche Schichtdicken können mit EBM-Systemen erreicht werden?
EBM-Maschinen können Schichten mit einer Dicke von bis zu 50 Mikrometern abscheiden. Dünnere Schichten von 25–35 Mikrometern sind typisch für kleine, komplizierte Komponenten, während 70–100 Mikrometer für größere, grobe Teile verwendet werden.
Welche Nachbearbeitungsmethoden werden für EBM-Komponenten verwendet?
Typische Nachbearbeitungen umfassen das Entfernen von Pulver, das Entspannen von Spannungen, das Abtrennen von der Platte, die maschinelle Bearbeitung, Oberflächenbehandlungen wie Schleifen oder Polieren sowie Inspektionen und Tests.
Welche Präzision und Oberflächenbeschaffenheit kann mit EBM-Teilen erreicht werden?
Eine Maßgenauigkeit von etwa ±0,21 TP3T (±0,5 mm pro 25 cm) ist erreichbar, die Toleranzen können jedoch durch Nachbearbeitung weiter verbessert werden. Die Oberflächenrauheit im gebauten Zustand liegt zwischen 10 und 50 μm Ra.
Wie schneidet EBM im Vergleich zu DMLS für Luft- und Raumfahrtanwendungen ab?
EBM kann die Materialeigenschaften traditionell geschmiedeter Titankomponenten für Strukturanwendungen erreichen. Es bietet höhere Aufbauraten als DMLS, erfordert jedoch in der Regel eine umfangreichere Nachbearbeitung.