Überblick über Additive Fertigungspulver
Pulver für die additive Fertigung sind Werkstoffe aus Metalllegierungen, die in Pulverform speziell für 3D-Druckverfahren wie selektives Laserschmelzen (SLM), direktes Metall-Lasersintern (DMLS), Elektronenstrahlschmelzen (EBM) und Binder-Jetting hergestellt werden. Die optimierten Partikelgrößenverteilungen, die Morphologie, die Chemie und die Pulvereigenschaften erleichtern das präzise, schichtweise Verschmelzen zu Endkomponenten.
Tabelle 1: Überblick über die Pulvereigenschaften bei der additiven Fertigung
Attribut | Beschreibung |
---|---|
Ausgangsstoff Material | Kugelförmige Teilchen aus einer Metalllegierung |
Produktionsmethoden | Gaszerstäubung, Elektrolyse, Carbonyl |
Verwendete Materialien | Titan, Aluminium, rostfreie Stähle, Superlegierungen, Werkzeugstähle |
Partikelgrößen | 10 - 45 Mikrometer typisch |
Wichtige Eigenschaften | Fließfähigkeit, Dichte, Mikrogefüge, Reinheit |
Primäre Anwendungen | Luft- und Raumfahrt, Medizin, Automobil, Industrie |
Dank der sorgfältigen Kontrolle von Merkmalen wie Partikelform, Größenverteilung, Chemie und Mikrostruktur fließen AM-Pulver reibungslos, packen dicht und verschmelzen konsistent Schicht für Schicht, um komplizierte, robuste metallische Komponenten mit mechanischen Eigenschaften zu schaffen, die denen herkömmlicher Herstellungsmethoden entsprechen oder sie sogar übertreffen.
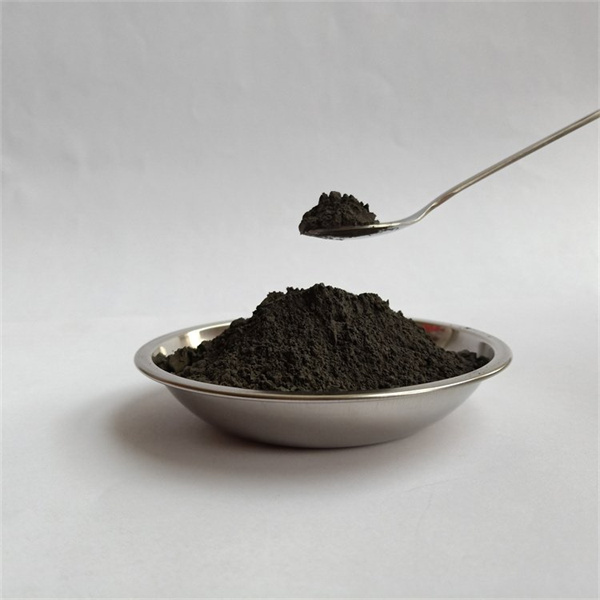
Metallpulver-Produktionsmethoden für AM
Bei additiv hergestellten Pulvern werden mehrere primäre Produktionsverfahren eingesetzt, um feine, kugelförmige Pulver mit der gewünschten Chemie, Kornbildung, Oberflächenmorphologie, Porosität und Partikelverteilung zu erzeugen, die für AM-Verfahren erforderlich sind.
Tabelle 2: Vergleich der Pulverherstellungsverfahren der Additiven Fertigung
Methode | Beschreibung | Pro/Kontra |
---|---|---|
Gaszerstäubung | Hochdruckgas bricht geschmolzenen Metallstrom in Tröpfchen auf | Einheitliche Partikel, Flexibilität der Legierung - Nachteil: höhere Kosten |
Plasma-Zerstäubung | Der Elektrodenlichtbogen schmilzt/zersetzt Metalle in Partikel | Sehr kugelförmiges Pulver, kleine Chargen |
Hydrid-Dehydrid | Durch Wasserstoffabsorption dekrepitiertes Legierungspulver | Sehr feine Pulver mit guter Fließfähigkeit, aber geringerer Dichte |
Elektrolyse | Von der Anode in Pulver aufgelöstes metallisches Ausgangsmaterial | Geringere Kosten, aber unregelmäßige, flockige Formen |
Mit dem Fortschritt der AM-Hardware, die feinere Auflösungen bis hinunter zu 20 Mikrometern ermöglicht, werden engere Pulverpartikelgrößenverteilungen zwischen 15 und 45 Mikrometern unabdingbar - dies erfordert eine bessere Anpassung der Gas- und Plasmazerstäubung, um kugelförmiges Meteoritenpulver zu ermöglichen, das sich ideal für eine dichte Packung und einen glatten Rake eignet.
Die Abstimmung der Produktionsroute auf die geplanten Anforderungen des AM-Prozesses gewährleistet optimale Pulverspezifikationen, die die Leistungsvorteile ausgleichen.
Arten von Pulvern für die additive Fertigung von Metallen
Verschiedene Metalllegierungen, die in Pulverform hergestellt werden, finden heute breite Anwendung in AM-Techniken, die von preiswerten Polymeren bis hin zu teuren hochfesten Superlegierungen reichen. Dies ist der erweiterten Designfreiheit zu verdanken, die die Konsolidierung von Teilen erleichtert und die Eigenschaften über die Grenzen des Gießens oder der Bearbeitung hinaus verbessert.
Tabelle 3: Gängige Metallpulver-Materialien, die für AM genutzt werden
Material Klasse | Legierungstypen | Beschreibung |
---|---|---|
Aluminium-Legierungen | AlSi10Mg, AlSi7Mg | Leichtbau in der Luft- und Raumfahrt, in der Automobilindustrie |
Titan-Legierungen | Ti-6Al-4V, Ti 6Al4V ELI | Hochfeste Implantate für die Luftfahrt und die Biomedizin |
Rostfreie Stähle | 304L, 316L, 17-4PH | Korrosionsbeständigkeit für maritime Hardware |
Werkzeugstähle | H13, Maraging 300 | Extrem harte Schneidwerkzeuge und Formen |
Nickel-Superlegierungen | Inconel 718, Inconel 625 | Turbomaschinen wie Luft- und Raumfahrtmotoren |
Exotische Legierungen | Kupfer, Kobalt-Chrom, Wolfram | Individuelle Kompositionen erweitern die Grenzen |
Die optimierte Pulverbettschmelzumgebung erleichtert die Verarbeitung traditionell schwieriger Materialzusammensetzungen jenseits konventioneller Fertigungshürden. Dies ermöglicht Innovationen in den Bereichen Wärmemanagement für elektronische Verpackungen, Öl- und Gasventile und -pumpen für extreme Umgebungen, Komponenten für den Automobilsport und Satellitenhardware.
Die sorgfältige Auswahl der optimalen Legierung unter Berücksichtigung der Designprioritäten Gewicht, Kosten, Festigkeit und Umweltverträglichkeit ermöglicht ideale additiv gefertigte Hochleistungsteile, die von herkömmlichen Verfahren nicht erreicht werden.
Wichtige Eigenschaften von Pulvern für die additive Fertigung
Um einen reibungslosen, effektiven Materialauftrag zu gewährleisten, der für die Herstellung dichter, fehlerfreier gedruckter Bauteile entscheidend ist, müssen Pulverprodukte für die additive Fertigung strenge Anforderungen in Bezug auf ihre Fließeigenschaften, Schüttdichten, Restporositäten, Mikrostrukturen und Kontaminationsgrenzen erfüllen.
Tabelle 4: Typische Eigenschaften von Metall-AM-Pulvern
Charakteristisch | Typische Werte | Testmethoden | Bedeutung |
---|---|---|---|
Morphologie des Pulvers | Glatt, nahezu sphärisch | SEM-Bildgebung | Pulverbettpackung und -fluss |
Partikelgrößenverteilung | 10μm - 45μm | Laserbeugungsanalyse | Ebenenauflösungen, Baugeschwindigkeiten |
Schein- und Klopfdichten | 65-80% bzw. 80-92% | Gravimetrische Messungen über Hall-Durchflussmesser | Druckauflösung und -qualität |
Durchflussmengen | 23-33 Sekunden für 50 g | Zeitlich begrenzte Trichtertests | Streuleistung des Pulvers |
Verbleibende Porosität | <1% | Gaspyknometrie | Dichte und mechanische Eigenschaften |
Ox/N-Kontamination | <1000 ppm / <500 ppm | Inertgas-Analyse | Wiederverwendung des Pulvers, Vermeidung von Rissbildung im Prozess |
Die Überprüfung kritischer Pulvereigenschaften während der Produktion mit Hilfe fortschrittlicher Messgeräte erleichtert die Wiederholbarkeit und die Überwindung von Eigenschaftsabweichungen von Charge zu Charge durch statistische Prozessanpassungen in Echtzeit.
Die Abstimmung von gut charakterisierten Pulvern mit stabilen Entstehungsprozessen und engen Maschinentoleranzen gewährleistet zuverlässige AM-Produktionsläufe.
Spezifikationen für Pulver zur additiven Fertigung von Metallen
Um qualitativ hochwertige Komponenten aus AM-Hardware-Systemen zu gewährleisten, müssen Metalllegierungspulver im Vergleich zur herkömmlichen Pulvermetallurgie, die nur für die Verdichtung und das Sintern bestimmt ist, strengeren chemischen Kontrollen und Maßverteilungen entsprechen.
Tabelle 5: Typische Additiv-Pulver-Spezifikationswerte
Parameter | Gemeinsamer Bereich | Prüfverfahren | Bedeutung |
---|---|---|---|
Partikelgrößenverteilung | 15μm - 45μm | Laserbeugung | Steuert die Mindestauflösung des Merkmals |
Elementare Verunreinigungen | <1000 ppm | ICP-Spektroskopie | Verhältnisse der Wiederverwendung des Pulvers |
Scheinbare Dichte | 65-85% theoretisch | Gravimetrische Analyse mittels Hall-Durchflussmesser | Beeinflusst die mechanische Leistung |
Dichte des Gewindebohrers | 80-95% theoretisch | Gravimetrische Analyse | Packungsverhältnisse der Schichten |
Hall-Durchflussmenge | <40 Sekunden für 50 g Pulver | Zeitgesteuerter Trichtertest | Streukonsistenz des Pulverbettes |
Partikelform | >80% kugelförmig | SEM-Bildgebung | Gleichmäßigkeit der Fluidisierung im Kraftwerksbett |
Verbleibende Porosität | <1% | Gaspyknometrie | Dichte und mechanische Eigenschaften |
Die Überwachung der fortschrittlichen Formeln für den Gleichförmigkeitskoeffizienten und das Fließratenverhältnis, die für Metall-AM-Pulver entwickelt wurden, bietet tiefere Einblicke als der einfache Hall-Fluss allein und gewährleistet eine zuverlässige Anwendungsleistung.
Und durch die spezielle Anpassung der Größenverteilung erleichtern chemische Pulverlieferungen aktiv Prozessverbesserungen, die zu feineren Auflösungen, schnelleren Fertigungsgeschwindigkeiten und längeren ununterbrochenen Produktionsläufen führen, die für die Einführung von AM entscheidend sind.
Güteklassen und Normen für Pulver zur additiven Fertigung
Mit dem Vordringen der additiven Fertigung in regulierte Umgebungen in den Bereichen Luft- und Raumfahrt, Medizin, Automobil und Industrie werden standardisierte Methoden zur Spezifikation, Prüfung, Zertifizierung und Kontrolle von Metallpulvern unerlässlich, um Wiederholbarkeit, Qualität und Sicherheit zu gewährleisten.
Tabelle 6: Aufkommende Normen für Metall-AM-Pulver
Standard | Umfang | Zweck |
---|---|---|
ASTM F3049 | Standardleitfaden für die Charakterisierung von AM-Pulvern | Festlegung von Benchmark-Prüfmethoden zur Bewertung gängiger Pulvereigenschaften |
ASTM F3056 | Spezifikation für Nickellegierungspulver | Chemie, Herstellung, Häufigkeit der Wiederholungsprüfung |
ASTM F3301 | Praxis für sekundäre Prozessmethoden bei AM-Teilen | Spezifizieren Sie akzeptable Nachbearbeitungstechniken |
AS9100 rev D | Zugelassene Lieferanten für die Luft- und Raumfahrt | Qualitätssysteme für regulierte Industrien |
ISO/ASTM 52921 | Standardterminologie für AM - Abstimmung mit globalen Normen | Sicherstellung einer einheitlichen Terminologie und Spezifikation für AM-Pulvermaterialien |
Mit der zunehmenden Verbreitung von AM in der Handels- und Verteidigungsindustrie, die eine strenge Verifizierung und Rückverfolgbarkeit von Teilen erfordert, werden standardisierte Prüfverfahren, Dokumentation der Lieferkette, Stichprobenraten, Umgebungskontrollen in den Einrichtungen und Personalschulungen vorgeschrieben. Die Einhaltung der Vorschriften stellt sicher, dass die Anwender über einen vollständigen Materialstammbaum und Prozesstransparenz verfügen, was die in kritischen Anwendungen erwartete strenge Qualifikation erleichtert.
Regierungsbehörden unterstützen auch die laufende Entwicklung von Materialspezifikationen, Testtechniken und Best Practices, da sich AM auf verschiedenen Märkten weiterentwickelt. Die Zusammenarbeit zwischen Pulverherstellern, Drucker-OEMs und industriellen Anwendern wird weiterhin zu einem besseren Benchmarking führen und die Leistung und Zuverlässigkeit in der Praxis verbessern.
Anwendungen von Metallzusatzpulvern
Dank der zunehmenden Leistungsfähigkeit der Druckersysteme und der Verfügbarkeit optimierter Pulver für AM-Bedürfnisse verändert die additive Fertigung die Produktionswirtschaft in zahlreichen Branchen, von der Luft- und Raumfahrt bis hin zu Konsumgütern.
Tabelle 7: Primäre Anwendungen von Metallpulvern für die additive Fertigung
Sektor | Beispiel für einen Herstellungsprozess | Kosten-/Leistungsvorteile |
---|---|---|
Triebwerke für die Luft- und Raumfahrt | Düsen und Verteiler aus Inconel 718 über DMLM | Verkürzte Vorlaufzeiten, verbessertes Buy-to-Fly-Verhältnis |
Luftfahrt-Turbinen | Ti64-Strukturklammern über EBM | Gewichtseinsparung, Teilkonsolidierung |
Biomedizinische Implantate | Kobalt-Chrom-Orthopädie durch DMLS | Erhöhte Knochenintegrationsraten |
Autorennen | Kundenspezifische Legierungen und Geometrien durch SLM | Hohe Wärme-/Vibrationsbeständigkeit und Gewichtseinsparung |
Luxus-Uhren | Mikrokomponenten aus Gold und Stahl durch SLM | Design- und Gestaltungsfreiheit und schnelle Iterationen |
Dank erweiterter Materialoptionen und größerer verfügbarer Fertigungsvolumina überwindet Metall-AM die Produktionsbarrieren herkömmlicher Verfahren - es ermöglicht eine höhere Festigkeit, Leichtbau, verbesserte Hitzebeständigkeit durch generative Kühlkanäle, Bauteilkonsolidierung und kürzere Gesamtdurchlaufzeiten.
Diese Fertigungsvorteile fördern die Einführung von AM-Techniken, die die herkömmliche Produktion in allen kostensensiblen Branchen verdrängen, sobald die Wirtschaftlichkeit der Skalierung erreicht ist. Kontinuierliche Materialinnovationen versprechen eine Ausweitung der Anwendungen auf weitere extreme Umgebungen mit Chemikalien, Druck, Korrosion und Belastungen.
Lieferanten von Metall-AM-Pulvern
Eine breite Palette von Pulverherstellern liefert heute spezialisierte Metallwerkstoffe für den Bedarf an additiven Fertigungsverfahren für kleinere Auftragsfertiger bis hin zu großen Tier-1-Anbietern in der Luft- und Raumfahrt und innovativen Unternehmen für kundenspezifische Legierungen, die an die Grenzen der AM-Fähigkeiten stoßen.
Tabelle 8: Führende Anbieter von Metallpulvern für Additive
Unternehmen | Portfolio | Beschreibung |
---|---|---|
Praxair | Titan-, Nickel- und Kobalt-Legierungen | Führender Hersteller von zerstäubten Gasen und Pulvern |
Sandvik | Rostfreie Stähle | Hochleistungslegierungen, einschließlich Duplex- und Maraging-Stähle |
LPW-Technologie | Aluminium, Titan, Nickellegierungen | Kundenspezifische Legierungen und Bindemittelprodukte |
Zimmerer-Zusatzstoff | Werkzeugstähle, nichtrostende Stähle | Maßgeschneiderte Legierungen, die das Know-how der Stahlerzeugung nutzen |
AP&C | Titan, Nickelsuperlegierungen | Anbieter von Lösungen für den gesamten Lebenszyklus des Pulvers |
Hoganas | Rostfreie Stähle | Hochleistungslegierungen, einschließlich Duplex- und Maraging-Stähle |
Diese führenden Pulverhersteller arbeiten in der AM-Industrie aktiv mit Drucker-OEMs, Forschern und Normungsgruppen zusammen, um die Wiederholbarkeit der Abmessungen zu verbessern, die Porosität zu reduzieren und die Ästhetik und die mechanischen Eigenschaften der fertigen Komponenten zu verbessern.
Kostenanalyse für Metall-AM-Pulver
Die Preise für gängige Metall-AM-Pulver variieren je nach Zusammensetzung, Produktionsweg, Vertriebsstufe, Prüfanforderungen und Abnahmemenge erheblich, liegen aber im Allgemeinen deutlich über denen für herkömmliche Pulver für Press- und Sinteranwendungen.
Tabelle 9: Preise für Metalladditiv-Pulver
Material | Preisspanne | Kostentreiber |
---|---|---|
Aluminium-Legierungen | $50-120 pro kg | Geringere Metallkosten, aber hohe Kosten für den Gaszerstäuber |
Rostfreier Stahl | $50-200 pro kg | 316L ist teurer als die Sorten 17-4 oder 15-5 |
Werkzeugstähle | $60-220 pro kg | Höhere Kosten für Legierungselemente |
Titan-Legierungen | $200-600 pro kg | Verarbeitungsintensive Extraktion und Handhabung |
Nickel-Superlegierungen | $200-1000 pro kg | Geringe Elementausbeute und Fähigkeit zum rissfreien Drucken kritischer |
Exoten wie Ta oder W | $500-2000 pro kg | Derzeit sehr geringe Verfügbarkeit der globalen Produktion |
Die Preisvorteile gegenüber herkömmlichen Pulvern ergeben sich aus den viel geringeren Chargengrößen, den höheren Materialeinsatzkosten und den Unterschieden in der Verarbeitung, die Eigenschaften wie Sphärizität und kontrollierte Chemie optimieren, was die Anforderungen von AM erleichtert.
Mit der zunehmenden Verbreitung von Druckern, einem stärkeren Wettbewerb und einer größeren Fertigungstiefe werden die Kosten wahrscheinlich über 5-10 Jahre hinweg schrittweise sinken - entsprechend der typischen Roadmap für die technologische Reife. Allerdings werden die Preise für Spezialqualitäten aufgrund der Dynamik des Marktes für Metalle weiterhin deutlich höher liegen.
FAQ
F: Wie werden gebrauchte/recycelte Metall-AM-Pulver für weitere Druckzyklen aufgefrischt?
A: Die Pulver werden gesiebt, um große Partikel von mehr als 100 Mikrometern zu entfernen, chemisch ausgeglichen, um den Sauerstoff-/Stickstoffgehalt wiederherzustellen, und mit anteiligen neuen Materialien gemischt, um eine geeignete Wiederverwendung zu gewährleisten, ohne die Qualität der gedruckten Teile zu beeinträchtigen.
F: Welche kritischen Spezifikationen unterscheiden sich am meisten zwischen AM- und herkömmlichen Presspulvern?
A: Engere Partikelgrößenverteilungen von durchschnittlich 25 Mikrometern, höhere Schütt- und Klopfdichten, glattere sphärische meteoritische Pulverformen und niedrigere Sauerstoff- und Stickstoffgehalte unterscheiden die AM-Bedürfnisse von der traditionellen Pulvermetallurgie, die nur engere Toleranzen erfordert. Das Erreichen dieser optimierten Eigenschaften erleichtert den fehlerfreien AM-Druck.
F: Wie oft können gängige AM-Pulverlegierungen normalerweise wiederverwendet werden?
A: Ähnliche Titan- und Nickelsuperlegierungen erreichen bis zu 20 Zyklen, bevor sie mit frischem Pulver aufgefüllt werden müssen. Weniger teure nichtrostende Stähle können 50+ Wiederverwendungszyklen erreichen. Bei Aluminium und hochreaktiven Stählen ist die Recyclingdauer auf weniger als 5 Zyklen begrenzt.
F: Welches Potenzial zur Verbesserung der Eigenschaften haben AM-Pulver aus Metall im Vergleich zu herkömmlichen Materialien?
A: Die Kombination von hohen Festigkeits-/Gewichtsverhältnissen durch Ausdünnen/Hohlprofile mit eingebetteten Kanälen, die den Flüssigkeitsfluss, die Wärmeübertragung oder die strukturelle Verstärkung erleichtern, ermöglicht generative Designkonfigurationen, die die Herstellung von Komponenten revolutionieren, die mit subtraktiver Bearbeitung oder einstufigen Gussverfahren allein nicht möglich wären.
F: Welche Industriekategorien versprechen derzeit das größte Wachstum für Metall-AM-Pulver?
A: Die Luft- und Raumfahrt, die Medizintechnik, die Automobilindustrie und die Öl- und Gasindustrie sind dank hochwertiger Komponenten, die F&E-Investitionen rechtfertigen, führend in der frühen Mainstream-Expansion. Längerfristig wird jedoch eine Masseneinführung erwartet, die die Haltbarkeit von Konsumgütern verbessert und die Vorteile der AM-Flexibilität nutzt, da die Systemkosten sinken.