Overview of Molybdenum Metal Powders
Molybdenum powder is a refractory metal material produced from molybdenum metal, known for its extremely high melting point, strength at high temperatures, and resistance to wear and corrosion. Key properties make molybdenum powder an ideal choice for manufacturing parts and composites across industries like aerospace, defense, automotive, and power generation.
Table 1: Overview of Molybdenum Powder
Attribut | Beschreibung |
---|---|
Zusammensetzung | >99% pure molybdenum |
Wichtige Eigenschaften | High strength, hardness, heat/corrosion resistance, lubricity |
Produktionsmethoden | Gas atomization, electrolysis, carbonyl process |
Partikelgrößen | 1 – 100 microns |
Main Applications | Alloying agent, thermal spray powders, 3D printing |
With the second highest melting point among pure metals at 2623°C and strength maintained even above 2000°C, molybdenum offers unique advantages for demanding environments. Combined with excellent corrosion resistance and lubricity even at elevated temperatures, moly powders deliver unmatched performance capabilities to powder metallurgy applications across industries.
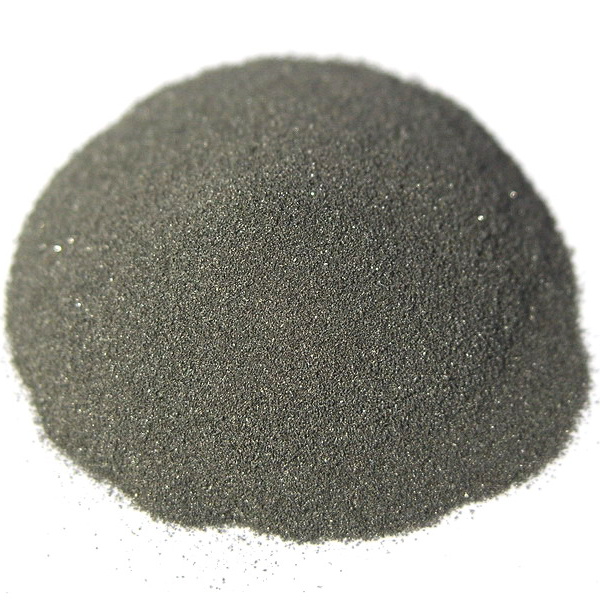
Types of molybdenum powders
Molybdenum powders are commercially produced in various forms using gas atomization, electrolytic, or carbonyl decomposition processes. These production techniques yield different particle size distributions, shapes, and purity levels tailored towards major application categories.
Table 2: Major Types of Molybdenum Powder
Typ | Beschreibung | Typische Verwendungen |
---|---|---|
Zerstäubtes Gas | Spherical powders from 5-100 microns | Thermal spray, MIM alloys |
Elektrolytische | Irregular flakes from 1-10 microns | Sintered parts, electronics |
Carbonyl | Spherical <1 micron, highest purity | Chemical/metallurgical applications |
Zerstäubtes Gas powders with adjustable morphology and tight particle distributions represent the most widely adopted type thanks to suitability for pressing, additive manufacturing, thermal spraying, and alloying.
Meanwhile, ultrafine carbonyl moly powders produced through decomposition serve niche applications needing high chemical purity like metallurgical additives or catalysts. The high surface area also suits sintering applications, though costs limit adoption.
Understanding application requirements facilitates appropriate molybdenum powder specification for optimal performance.
Properties of Molybdenum Metal Powders
Molybdenum powders deliver an exceptional combination of mechanical, thermal, electrical, and chemical properties elevating performance in challenging operating environments.
Table 3: Overview of Molybdenum Powder Properties
Eigentum | Wert | Bedeutung |
---|---|---|
Schmelzpunkt | 2623°C | Retains strength and hardness at high temperatures |
Dichte | 10.22 g/cc | Enables heavy alloy formulations |
Stärke | 500 MPa (73 ksi) | Withstands high mechanical loads |
Wärmeleitfähigkeit | 138 W/mK | Heat spreading ability |
Elektrischer Widerstand | 5.7 microOhm-cm | Electronics thermal management |
Coefficient of friction | 0.1-0.3 | Retains lubricity in vacuum environments |
Key attributes like high temperature strength, corrosion resistance, low friction, and thermal/electrical conductivity satisfy critical performance demands across potentially revolutionary powder metallurgy applications.
Additionally, the high density coupled with 100% recyclability makes molybdenum an ecologically friendly and sustainable metal choice relative to competing rare earth elements. This could disrupt elements like cobalt or tungsten in batteries, magnets, medical devices, aerospace components, and other products.
Understanding how properties like strength, melting point, density, resistivity, hardness evolve during sintering facilitates appropriate powder specifications and processing parameters for optimal in-service behavior.
Produktionsmethoden für Molybdän-Pulver
Commercial molybdenum powder utilizes three primary production routes to achieve the desired particle size, morphology, purity levels, crystal structure, and powder properties demanded by customers.
Table 4: Comparison of Molybdenum Powder Production Routes
Methode | Beschreibung | Typical Purity | Kosten-Faktoren |
---|---|---|---|
Gaszerstäubung | Inert gas disintegrates molten stream | >99% Mo | Pricing follows moly prices, high purity commands premium |
Elektrolyse | Anode dissolution into powder flakes | 99.8%+ Mo | High electricity consumption, low material yields |
Carbonyl-Verfahren | Thermal decomposition into fines | 99.99%+ Mo | Tightly controlled process, limited number of producers |
Gaszerstäubung delivers the widest range of powder sizes and morphologies making it the most widely adopted powder type across commercial and research domains.
Meanwhile the carbonyl process generates extreme purity needed for specialized chemical process applications where contamination poses risks.
Selecting appropriate production methods requires balancing factors like cost, particle characteristics, purity requirements, and availability.
Specifications of Molybdenum Powder Products
Molybdenum powders must satisfy strict property specifications related to composition, particle size distribution, morphology, purity levels, crystal structure, and microstructure. Manufacturers utilize advanced quality control tools to verify powder conformity.
Table 5: Typical Molybdenum Powder Specifications
Parameter | Typische Spezifikation | Prüfverfahren |
---|---|---|
Partikelgrößenverteilung | Per customer request (1-100 microns) | Laser diffraction particle analyzer |
Chemie | >99% molybdenum | ICP mass spectrometry |
Sauerstoff/Stickstoff | < 500 ppm | Analyse der Inertgasfusion |
Morphologie | Sphärisch | SEM-Bildgebung |
Reinheit | 99.9% to 99.9999% | GDMS trace element analysis |
Scheinbare Dichte/Hahndichte | 35 to 50% / 65 to 80% theoretical | Hall flowmeter funnel |
Kristallstruktur | BCC | Röntgenbeugung |
Controlling powder characteristics like flow, apparent and tap densities, oxygen/nitrogen levels, and microstructural phases ensures optimal powder spreading, compacting, sintering, and final part performance.
Molybdenum producers continually enhance quality assurance efforts through procedures like:
- Statistical process control monitoring of critical parameters
- Data analytics on sampling rates and test frequencies
- Employee training for contamination prevention
- Certifications to standards like ISO 9001:2015, AS9100D, ISO 13485
This drives continual improvements in product consistency, traceability, and customer specifications conformance across medical, aerospace, defense, and industrial market segments.
Grades and Standards for Molybdenum Powder
As a widely used engineering material across applications like aerospace, oil & gas, defense, and power generation, molybdenum powder products must satisfy various purity grades and national/international standards.
Table 6: Common Grades and Standards for Molybdenum Metal Powders
Standard | Beschreibung | Required Properties |
---|---|---|
ASTM B939 | Covers electrolytic moly powder specification | >99.8% Mo, oxygen limits, particle size distribution |
SAE AMS 7871 | Aerospace material specification for gas atomized powder | Chemistry, particle size distribution, apparent density |
ISO 21109 | Sets requirements for plasma spray grade powder | Particle size distribution, flow rates |
Custom grades | Application-specific powder variants | Per individual customer requirements |
Additionally, national bodies like ASTM International and professional trade groups support ongoing development around material specifications and test methods as the applications for molybdenum powders continue advancing across industries.
Research collaborations between material manufacturers, part fabricators in MIM and AM, and end-use customers also facilitate qualification of custom powder grades optimized around factors like alloying additions, particle size ranges, or contaminant limits.
Applications of Molybdenum Metal Powders
Thanks to an exceptional balance of extreme temperature strength, wear/corrosion resistance, thermal conductivity, lubricity, and environmental stability, molybdenum powders enable breakthrough performance enhancements across a variety of industries.
Table 7: Major Applications for Molybdenum Powders
Anmeldung | Beschreibung | Benefits vs Alternatives |
---|---|---|
Alloying agent | Added to steels and superalloys | Strength and hardness at high temperatures |
Thermische Spritzschichten | Wear resistant films against corrosion/erosion | Superior hardness and lubricity over chromium carbide alternatives |
Sintered PM parts | Net shape fabrication of components | High strength above 1800°C vs tungsten |
Elektronik | Thermal management of devices/processes | Double conductivity of aluminum alternatives |
Kernreaktoren | Extreme temperature parts | Retains structural stability over chromium/tantalum options |
Expanding research and development efforts focus on unlocking new possibilities for molybdenum metal powders across areas like:
Oil and Gas Exploration
- Downhole tools and drilling equipment resisting corrosion/wear
- Valves and seals for high pressure pumps
Automotive/Aerospace
- Pistons, engine, and exhaust parts handling extreme temperatures
- Lightweighting opportunities over dense alloys
Medizinische
- Implants leveraging biocompatibility and high strength
- Surgical tools withstanding repeated sterilization
3D-Druck
- Custom alloy formulations using moly powder tailoring properties
- Refractory metals support structures
The unique thermal, mechanical, electrical, and environmental stability of molybdenum makes this sustainable material a primary candidate for innovations across powder metallurgy techniques over the coming decade.
Popular Suppliers of Molybdenum Metal Powders
Many leading metal powder producers offer molybdenum powder compositions to satisfy needs across niche research applications through high volume commercial sectors. Both major multi-metal suppliers and specialized molybdenum processors are active in this market.
Table 8: Leading Molybdenum Powder Manufacturers
Unternehmen | Beschreibung | Produktionskapazitäten |
---|---|---|
H.C. Starck Lösungen | Broad Mo powder portfolio incl. custom alloys | All major production routes at multi-ton annual scale |
Molymet | Top molybdenum chemical and powder processor | High purity moly oxides, carbides, nitrides beyond metals |
JDC | Japanese powder leader with atomizing and electrolytic capability | Range of stainless, alloy steels with moly powder focus |
Plansee | Refractory metal powder expertise | Custom alloy development around Mo, W, Ta systems |
Mi-Tech Tungsten Metals | Primary US producer of tungsten and moly powders | Electrolytic moly flakes, oxides, other compounds |
These industry leaders continue investing in production capacity, quality improvements, and new composition developments to serve the latest application demands as adoption of molybdenum powders accelerates across medical, aerospace, automotive, and industrial categories over the next five years.
Cost Analysis for Molybdenum Powder
As a specialized minor metal, molybdenum powder prices fluctuate with market dynamics around supply and demand. However, moly powder maintains a substantial cost advantage over rival refractory metals like tungsten and tantalum.
Table 9: Molybdenum Powder Cost Analysis
Parameter | Typischer Bereich | Drivers |
---|---|---|
Molybdenum metal price | $25-40 per kg | Raw mineral supply/demand swings |
Molybdenum powder | $50-150 pro kg | Purity grade, production route, distribution channel |
Wolfram-Pulver | $50-250 per kg | Lower output than China, limited suppliers |
Tantalum powder | $400-1000 per kg | Very rare mineral supply |
As an example, molybdenum powder with 99.9% purity sells for approximately $60 per kg in bulk volumes using gas atomization methods. Meanwhile, extra low oxygen variant with 99.99% purity commands over 2X premium to $140 per kg.
Compared to tungsten and tantalum powders, molybdenum maintains significant cost advantages thanks to larger mineral reserves and higher mining output levels. This enables molybdenum powder solutions to displace rival refractory metal choices across automobile, aerospace, industrial heating, and even medical implant categories.
Within the next decade, rising market adoption stemming from moly powder’s unique balance of extreme temperature properties, fabrication versatility, and economic viability points towards supply deficits barring major capacity expansions. This likely suggests higher prices beyond current cyclical commodity downturns as demand growth outpaces mining production growth.
Future Outlook for Molybdenum Powder Adoption
Expanding research and commercialization efforts focused on leveraging molybdenum’s exceptional balance of properties points towards significantly broader adoption of moly-based powder alloys across transportation, energy, medical, defense, and industrial heating categories.
Market analysts predict global demand for molybdenum metal and alloys growing over 6% CAGR over the next 5 years as new applications displace legacy alloys and hard-to-machine materials. In particular, powder metallurgy fabrication routes like metal injection molding, additive manufacturing, and thermal spraying of molybdenum alloys appear positioned for above average expansion compared to milled product forms.
However, sustainable supplies of raw molybdenum minerals could face strains matching pace with rapid demand expansion from energy and industrial sectors without significant mining capacity growth. While currently enjoying a cyclical downturn, longer term fundamentals support renewed upward pricing pressures on moly products by the middle of the decade barring substantial new mining projects.
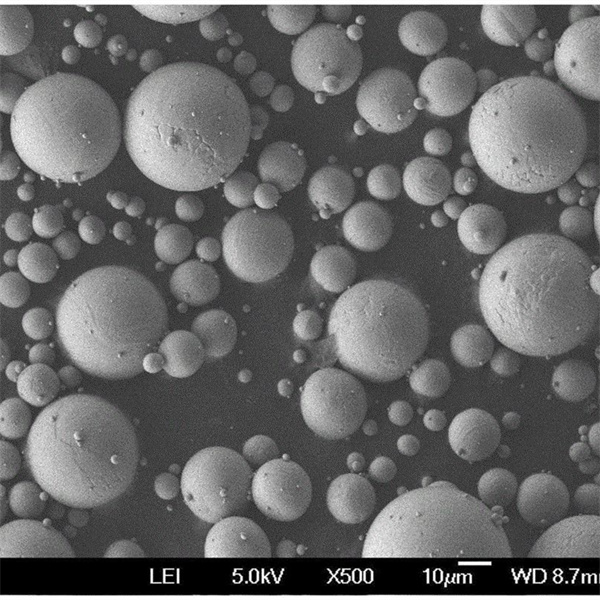
FAQ
Q: What alloying elements mix best with molybdenum powders?
A: Nickel, chromium, silicon, boron, carbon, and cobalt are common alloyants for enhancing sinterability, strength, hardness, or high temperature creep resistance depending on application aims.
Q: What particle size range works best for sintering molybdenum powder?
A: Gas atomized molybdenum powders between 5 to 25 microns show optimal pressing and sintering behavior for most fabricated component applications.
Q: How difficult is molybdenum powder to process using AM methods?
A: Careful parameter development for laser/electron beam systems is vital to control defects like curling, porosity issues, or microcracking. Hot isostatic pressing helps maximize densities and mechanical performance.
Q: Why is high purity important for molybdenum powders?
A: Contaminants like oxygen, nitrogen, and carbon shift ductile-to-brittle transition temperatures significantly, reducing fabricability and inducing spontaneous cracks during printing or sintering. Tighter chemistry control minimizes such issues.
Q: What applications pose corrosion risks for molybdenum powder products?
A: Saltwater, acidic sulfur/chloride compounds, and molten zinc attack molybdenum. Small alloying additions of chromium, nickel, or cobalt improves corrosion resistance. Protective coatings also mitigate concerns in problematic environments with regular maintenance.